Star-Delta Motor
When the electric motor is started, it attracts a high current typical 5-6 times larger than the traditional currencies.
In DC motors there’s no back voltage at the beginning so the initial current is incredibly high as compared to the conventional current.
To protect the motor from these high beginning currents we tend to use a star and delta starter.
Simply in Star affiliation, the provision voltage to the motor is less. therefore we tend to use star affiliation throughout the beginning of the motor when motor running, we’ll amendment the affiliation type star to delta to realize the full speed of the motor.
Star Delta Motor Starter
The following figure shows the winding connections in star and delta configuration one by one.

It is often seen that in star association, one finish of all 3 windings area unit shorted to create star purpose whereas the opposite finish of every winding is connected to the ability provide.
In delta configuration, the windings area unit connected such to create a control system.
The association of every winding is shown within the on top of the figure. In associate actual motor, the three-phase connections area unit provided within the following order as shown.
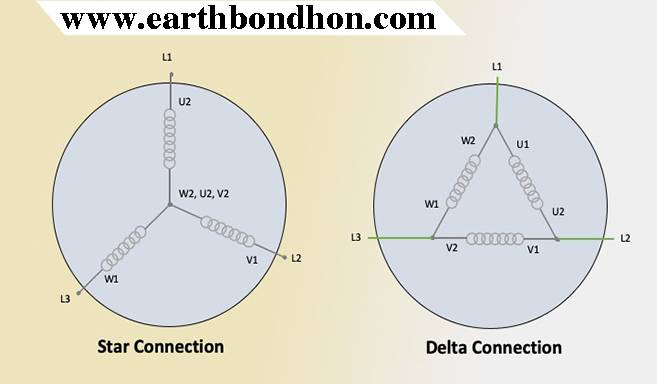
So in order to make the winding connection in star and delta style in practical motor, the connection is shown above.
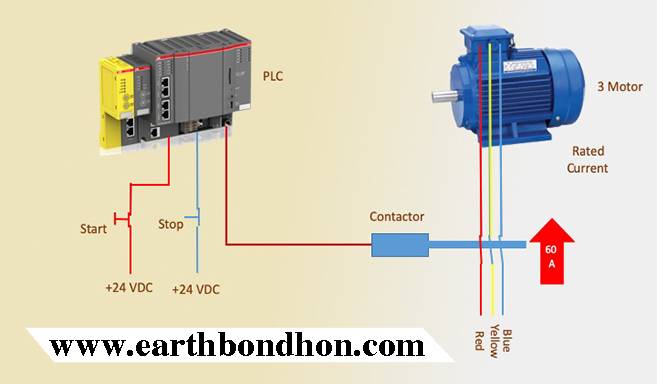
The main contractor is employed to activity power to the windings. It should be turned on all the time. Initially, the star contactor is closed whereas the delta contactor is open It makes the motor windings during a star configuration.
When the motor gains speed, the star contactor is opened whereas the delta contactor is closed turning the motor windings into delta configuration.
The contactors square measure controlled by exploitation PLC. the subsequent section of the PLC tutorial can justify the ladder programming for star delta motor starter.
PLC program for star delta motor starter :

Rung one Main contactor :
The main contactor depends upon the ordinarily open input begin electric switch (I1), ordinarily closed stop button (I2) and ordinarily closed overload relay.
It means the most contactor can solely be energized if the beginning button is ironed, whereas the stop isn’t ironed and therefore the overload relay isn’t activated. An ordinarily open input named (Q1) is added in parallel to the beginning button I1.
By doing this, a push-button is made which implies that when the motor is started, it’ll be unbroken started even though the beginning button is discharged
Rung a pair of Star contactor:
Star contactor depends upon the most contactor, ordinarily closed contacts of timer (T1) and ordinarily closed contacts of output delta contactor (Q3).
So star contractor can solely be energized if the most contactor is ON, time output isn’t activated and delta contractor isn’t energized.
Timer T1:
Timer T1 measures the time when the winding association of star delta starter is to be modified. it’ll begin tally time when the most contactor is energized.
Rung three Delta contactor:
Delta contactor is energized once the most contactor (Q1) is energized, timer T1 is activated and star contactor (Q3) is de-energized.
Also, see Programing of push-button and different needs for the easy motor starter is explained in PLC Tutorial: Motor starter
Note: This post for academic or reference functions solely. For a live circuit, there’ll be some additions to the higher than circuit like protective, as per application, some interlocks, etc.